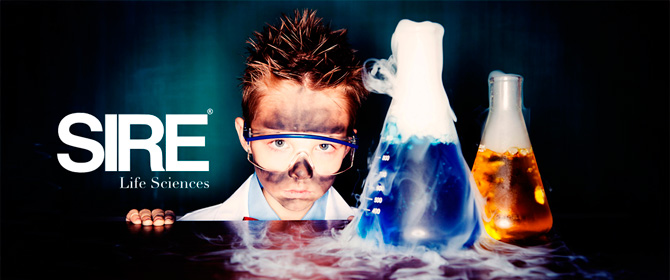
SR Manager, Quality Internal Audit
Location: NetherlandsSIRE Life Sciences® is the market leader in life science recruitment. We believe the recruitment market needs to gear up in technology and continues innovation. We like technology, in a life science market driven on science, we couldn’t stay behind; we drive Recruitment Science. Investing a majority of our turnover in technology enables us to use unique Resource Technologies. By using highly advanced algorithms, we enable our team of Resource & Data Strategists© to maintain the most advanced, detailed and complete Life Sciences network in Europe. This big data enables us to work Reverse Recruitment©: we first analyze the market in-depth before we go out to the market. Because we analyze the whole market, we can compare facts and data. This enables us to do Facts & Big Data Recruitment©, making sure we, or better yet, you find the right career!
THE COMPANY
Our client is a professional Medical Devices organization, based in Noord-Holland Netherlands.
My client is one of the world leading Medical Devices.
ROLE DESCRIPTION
- Working in partnership with the Global Supply Quality organisations audit group located at the manufacturing sites, you will
be responsible for the strategic planning, and management of quality audit program and post-processing of internal audit reports and data.
- Ensure that the audit programme for sites is performed in effective and efficient manner
- Ensure a dynamic audit process and program such that audits can focus on process and QMS, thus meeting compliance and product quality requirements.
- Ensure that the audit program is performed and addresses the requirements of 21CFR 820, ISO 13485, and other applicable standards to assess and ensure QSR compliance as it relates to manufacturing process and product specifications.
- Manage pre and post audit activities by involving all relevant stakeholders of different functions within Quality teams
- Identify and communicate to Quality leadership issues that impact product quality, safety or efficacy, regulatory compliance or business continuity which have arisen from an audit
- Provide Regional Headquarters (RHQ) Quality and Operations Management with periodical quality audit performance assessment and KPI’s of each manufacturing site,
- Provide SME input to enable risk to be assessed and as an input to the quality planning process
RESPONSIBILITIES
- Plan, Approve, Manage and continually assess the quality audit program, and its tactical execution carried out at the manufacturing sites
- Ensure continuous quality compliance through quality audit program for the Sites.
- Enable Standardised and consolidated internal audit planning and management activities, by developing effective and efficient quality audit business process at the RHQ
- Leverage greater efficiencies in the audit group by applying standardised/harmonised methodologies to quality audit activity management and tactical execution at the manufacturing sites
- Ensure effective closure of audit findings, by mentoring and coaching auditors and auditees to ensure comprehension, development, and execution of corrective/preventive action with regards to any nonconformity cited during audits.
- Create a formal audit reporting program which ensures the timely completion of audit reports, the assignment associated corrective actions, and the performance measurement of audit activities and closure of actions from audit results
- Ensure the audit program adapts to changes to both internal and external quality requirements and changes.
- Conduct and support quality benchmarking activities.
- Identify areas of opportunity and support continual improvement of Quality and work with the relevant groups on how these can be improved.
- Collaborate with the co-ordination of external body audit activities at the manufacturing sites
- Actively develop the team’s expertise and team dynamics through continuous coaching, promoting development programmes and formal appraisals through the IPMPD review process
REQUIREMENTS
- Bachelor’s degree in Science, Engineering or related subject , 8+ years relevant quality experience in GMP manufacturing environment in Medical Device/Pharma industry.
- Thorough knowledge of current regulations, pertinent regulatory guidance and industry trends.
- An understanding of the technical aspects of the areas being audited – understand the process, operational terminology etc.
- Experience in quality management systems is essential.
Special skills:
- Must possess strong communication, project management and leadership skills as well as have the ability to manage multiple projects simultaneously.
- Strong interpersonal skills.
- Strong leadership skills.
- Strong written and oral communication and negotiations skills.
- Highly developed problem solving skills.
- Strong analytical skills.
- Demonstrated ability to successfully manage and complete projects in a matrix organization.
- Demonstrated ability to lead cross-functional teams.
- Demonstrated ability to work independently.
- Demonstrated knowledge of U.S. Food and Drug regulations, as well as of European and international regulatory/industry guidelines/standards, and ability to interpret and apply.
- Computer literacy.
- 30% travel required.
Are you interested and do want to apply for this role, please fill out your application via the apply button below and contact Tim Thuijs.
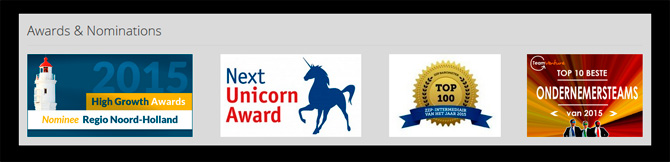